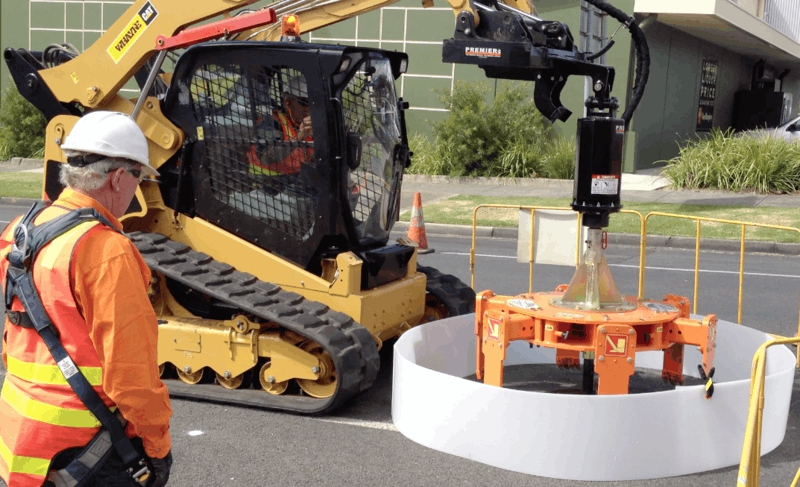
Cutting Edge Manhole Leveling & Coating System
We now proudly introduce Mr. Manhole Australia, a unique, cutting -edge complete solution for rebuilding, repairing and levelling manhole chimney sections.
Making it Better – Faster – Safer is the centre of our corporate philosophy at Mr. Manhole Australia. We believe that the pursuit of excellence is nothing short of doing it better than the last time and doing it faster and better than our competition. The cornerstone of this philosophy is safety. We believe that our workforce is the backbone of who we are and their safety is paramount.
Making it Better – Faster – Safer is a commitment to ourselves.
Combining Safety, Speed, and Quality – the winning trifecta!
When Barwon Water asked contractors John and Yvonne Smith if they could suggest a way of economically repairing damaged manhole covers in Geelong streets, they were at a loss to suggest anything until their son suggested they look at a website called Mr Manhole – and immediately a solution was in sight.
Award nominees have Australian first
Nominees in this year’s Earthmover & Civil Contractor Awards, John and Yvonne have subsequently introduced an innovative new process to Australia which allows them to replace manholes with a swift and simple method that has revolutionised this type of road repair.
As you will soon discover, the process is so impressive that it was nontinated for a Product Innovation Award this year and made it through as a finalist, pipped at the post by Caterpillar’s impressive D7E.
Manholes are traditionally repaired by using a concrete saw to cut a square around the offending access point, and then air hammers are used to break the surrounding concrete or bitumen. It is a slow, labour-intensive, imperfect process, which involves manually lifting heavy pre cast concrete rings.
But with the Mr Manhole System, a skid steer mounted circular cutter-extractor is used to quickly cut through and remove the manhole frame and the surrounding road material sometimes in as little as 10 minutes, without heavy lifting or manual labour.
A special plate is placed inside the man hole frame, and functions as a centre point for the Mr Manhole cutter-extractor. The cut ter enables a perfect round cut with full road penetration. The skid steer then uses the cut ter-extractor to lift the manhole frame and road overcut out. Once the manhole frame and road overcut are removed – the rebuild takes place.
The system will cut the liner to the appro priate slope and height of the road then epoxy coated rebar is placed and rapid set ting concrete poured to road level, eliminat ing the bump and leak problem and provid ing a long lasting structurally engineered repair.
John and Yvonne approached Barwon Water with the information they had discov ered and getting a favourable hearing, they proceeded to acquire the necessary equip ment from the US.
“We made an agreement with Mr Manhole in the US that we would promote the product and sell the equipment as well,” Yvonne said. The pair aims to set up a distribution and training centre in Geelong.
As they didn’t have a skid steer at the time, that became a priority (see breakout). So about six months after Barwon Water made their request for a manhole repair solu tion, the Smiths were set to implement the Mr Manhole way forward.
Barwon Water’s first replacement priority was to repair battered outfall sewer manholes along La Trobe Terrace in central Geelong. Cars would change lane a they “clunked” in Yvonne’s word . over depressed manholes.
The repair time lines were, and still are, quite strict. Permits to work are not available until 8pm and are issued with a requirement to have restored manholes ready to drive over by 6am the following morning.
That means – in effect – that manholes must be restored ready for concreting by 3.30am, so that fast setting concrete can be poured, screeded and sealed by 4am to allow a two hour setting process. Much of the con crete has been supplied by Volumetric’s mix and pour on-demand fast setting product, although for smaller jobs the company mixes their own.
Yvonne said that concrete did not vary a great deal in cut-ability but asphalt did.
“You can’t tell by looking at asphalt, but we’ve found some in Geelong which is extremely hard and some at the other end of the scale which is quite soft,” she said. Since March, Mr Manhole Australia has replaced 44 manholes for Barwon Water in Geelong, sometimes replacing four in one night.
“We were really under the pump to do four in a night though,” she said. They did 22 in La Trobe Terrace over about four weeks, “but not every night because we were not allowed to work on Friday nights.”
On La Trobe Terrace there was quite a bit of broken asphalt so they used the extended cutter arms to include that, but not quite to their maximum of 2.4 metres. About six weeks later, they completed about 22 more manholes in Mercer Street, using a different but more effective circle cutter.
The Smiths, trading as Geelong Waterproofing, have operated around Geelong for 19 years rehabilitating the interi or of corroded concrete Barwon Water pipes.
Yvonne said, “Barwon Water is over the moon with what we’ve done with the man holes. We had held off promoting the busi ness further afield until we gained market acceptance. But now we have that.”
Since they started with the Mr Manhole equipment, to make the operation more efficient, they have bought a John Deere backhoe, a tip truck, a low loader trailer and a special trailer to hold the Mr Manhole equipment.